СВЕДЕНИЯ О ДОКУМЕНТЕ
Источник публикации
М.: Госстрой России, ГУП ЦПП, 2001
Примечание к документу
Взамен
СП 478-80
.
Название документа
"СП 40-102-2000. Проектирование и монтаж трубопроводов систем водоснабжения и канализации из полимерных материалов. Общие требования"
(одобрен Постановлением Госстроя РФ от 16.08.2000 N 80)
"СП 40-102-2000. Проектирование и монтаж трубопроводов систем водоснабжения и канализации из полимерных материалов. Общие требования"
(одобрен Постановлением Госстроя РФ от 16.08.2000 N 80)
Одобрен и рекомендован к применению
Постановлением
Госстроя РФ
от 16 августа 2000 г. N 80
СИСТЕМА НОРМАТИВНЫХ ДОКУМЕНТОВ В СТРОИТЕЛЬСТВЕ
СВОД ПРАВИЛ ПО ПРОЕКТИРОВАНИЮ И СТРОИТЕЛЬСТВУ
ПРОЕКТИРОВАНИЕ И МОНТАЖ ТРУБОПРОВОДОВ СИСТЕМ
ВОДОСНАБЖЕНИЯ И КАНАЛИЗАЦИИ ИЗ ПОЛИМЕРНЫХ МАТЕРИАЛОВ
ОБЩИЕ ТРЕБОВАНИЯ
DESIGN AND INSTALLATION OF POLYMERIC PIPELINES FOR WATER
SUPPLY AND SEWAGE SYSTEMS.
GENERAL REQUIREMENTS
СП 40-102-2000
Группа Ж21
ОКС 91.140.60;
ОКСТУ 492000
Взамен
СН 478-80
Настоящий Свод правил содержит указания по проектированию и расчету систем трубопроводов наружного и внутреннего водоснабжения и канализации из труб из полимерных материалов. Выполнение этих указаний обеспечит соблюдение обязательных требований к наружным и внутренним системам водоснабжения и канализации, установленных действующими
СНиП 2.04.01-85*
"Внутренний водопровод и канализация зданий",
СНиП 2.04.02-84*
"Водоснабжение. Наружные сети и сооружения" и
СНиП 2.04.03-85
"Канализация. Наружные сети и сооружения".
Решение вопроса о применении данного документа при проектировании и строительстве конкретных зданий и сооружений относится к компетенции проектной или строительной организации. В случае если принято решение о применении настоящего документа, все установленные в нем правила являются обязательными. Частичное использование требований и правил, приведенных в настоящем документе, не допускается.
В данном Своде правил рассмотрены общие вопросы, касающиеся труб из различных полимерных материалов. Установлены общие требования к сортаменту труб и способам их соединения, рассмотрены вопросы монтажа трубопроводов, хранения труб и техники безопасности при их монтаже. Приведены методики гидравлического расчета систем водоснабжения и канализации, а также прочностного расчета напорных и безнапорных трубопроводов при подземной прокладке в грунте.
В разработке Свода правил принимали участие: Ю.Н. Саргин, А.Я. Шарипов (СантехНИИпроект), А.В. Сладков, А.А. Отставнов (ГУП НИИМосстрой), В.А. Устюгов, В.С. Ромейко, А.Я. Добромыслов, В.Е. Бухин, Л.Д. Павлов (ЗАО "НПО Стройполимер"), К.И. Зайцев (АО "ВНИИСТ"), В.А. Глухарев, В.П. Бовбель (Госстрой России), Л.С. Васильева (ГП ЦНС).
Настоящий Свод правил распространяется на проектирование и монтаж строящихся и реконструируемых систем внутренних и наружных сетей водоснабжения и канализации из труб и соединительных деталей (далее - трубы) из полимерных материалов.
2.1. Данный документ включает требования, общие для всех видов труб из полимерных материалов. Специфические требования для каждого вида трубопроводов из полимерных материалов приведены в соответствующих сводах правил.
2.2. Трубы, соединительные детали и элементы из полимерных материалов, применяемые в системах водоснабжения и канализации, уплотнительные материалы, вещества для смазки, клеи и пр. должны иметь сертификаты или технические свидетельства, а для систем водоснабжения - гигиенические заключения Госсанэпиднадзора Минздрава России.
2.3. Характеристики некоторых полимерных материалов, применяемых для производства труб и соединительных деталей, приведены в
Приложении А
.
2.4. Перечень нормативных документов, на которые даны ссылки в Своде правил, приведен в
Приложении Б
.
3. ПРОЕКТИРОВАНИЕ ВНУТРЕННИХ ВОДОПРОВОДНЫХ СЕТЕЙ
3.1.1. Выбор материала труб для систем холодного и горячего водоснабжения следует производить с учетом назначения и условий работы трубопроводов, температуры транспортируемой воды, а также срока службы трубопроводов, руководствуясь отдельными сводами правил на проектирование и монтаж тех или иных видов труб трубопроводных систем.
3.1.2. Трубы и соединительные детали из полимерных материалов, предназначенные для хозяйственно-питьевого водоснабжения, должны иметь в маркировке слово "Питьевая".
3.2.1. Тип труб и соединительных деталей (за исключением изготовленных из стеклопластика) для водопроводов холодной воды определяется по номинальному давлению в соответствии с таблицей 1.
Таблица 1
Тип трубы
|
Номинальное давление по ГОСТ 29324, МПа
|
Легкий Л
|
0,25
|
Среднелегкий СЛ
|
0,4
|
Средний С
|
0,6
|
Тяжелый Т
|
1,0
|
Особотяжелый ОТ
|
1,6
2,0
2,5
|
Напорные трубы из стеклопластиков подразделяются на три типа по номинальному давлению - 0,6; 1,6 и 2,5 МПа.
За номинальный диаметр трубопроводов, изготавливаемых методом экструзии, принят наружный диаметр. Для труб, изготавливаемых методом намотки (например, стеклопластиковые и базальтопластиковые), за номинальный диаметр принят внутренний диаметр.
Примечание. Номинальное давление - это постоянное внутреннее избыточное давление воды, которое трубы и соединительные детали могут выдерживать в течение всего срока эксплуатации (50 лет) при температуре воды 20 °С.
3.2.2. Напорные трубы из полимерных материалов и их соединения, применяемые для внутреннего водопровода горячей воды, должны быть рассчитаны на условия постоянного воздействия температуры воды 75 °С и расчетного периода эксплуатации не менее 25 лет.
3.2.3. Классификация напорных труб может производиться также по показателю "SDR" и по сериям "S". Определение этих показателей приведено в
Приложении А
.
3.3. Виды и способы соединения труб
3.3.1. Напорные трубы, предназначенные для внутренних водопроводов, должны соединяться в зависимости от вида полимерного материала:
- на сварке враструб (полиэтиленовые, полипропиленовые, полибутеновые и др.);
- на клею враструб (поливинилхлоридные, стеклопластиковые, базальтопластиковые и др.);
- механическим путем с помощью разъемных и неразъемных соединительных деталей (металлополимерные, "сшитого" полиэтилена и др.).
3.3.2. Способы соединения пластмассовых труб, соединительных деталей и арматуры и места их расположения устанавливаются проектом в зависимости от:
- назначения трубопровода;
- свойств материала;
- вида, номенклатуры и размеров труб, соединительных деталей и арматуры;
- рабочего давления и температуры транспортируемой воды;
- вида и свойств транспортируемого вещества;
- нормативного срока службы трубопровода;
- способа прокладки трубопровода и условий выполнения строительно-монтажных работ;
- температуры окружающей среды;
- планировочных решений.
3.3.3. Вид соединения следует принимать из условий обеспечения герметичности и прочности трубопровода на весь проектируемый срок эксплуатации, а также технологичности при монтаже и возможности ремонта трубопровода.
3.3.4. Разъемные соединения предусматриваются в местах установки на трубопроводе арматуры и присоединения к оборудованию и для возможности демонтажа элементов трубопровода в процессе эксплуатации. Эти соединения должны быть расположены в местах, доступных для осмотра и ремонта.
3.3.5. Соединение труб из разнородных несклеивающихся и несваривающихся модифицированных и композиционных полимерных материалов осуществляется с помощью механических соединений, конструкция и технология применения которых устанавливаются по данным их изготовителей и поставщиков для конкретного полимерного материала.
3.3.6. Металлические детали соединений должны быть изготовлены из коррозионно-стойкого материала.
3.3.7. Срок службы соединений должен соответствовать сроку службы труб.
3.4. Прокладка трубопроводов
3.4.1. Трассировка трубопроводов водопровода производится с учетом физических (химических) и механических свойств материала труб и способов их соединения и требований, указанных в
СНиП 2.04.01
.
При монтаже труб на сварке можно применять традиционные схемы прокладки водопроводов - кольцевые и тупиковые, при соединении труб с помощью соединительных деталей системы рекомендуется выполнять с применением коллекторных узлов с размещением в них запорной и регулирующей арматуры, узлов присоединения участков трубопроводов и приборов учета количества и расхода воды.
3.4.2. Трубопроводы, как правило, должны прокладываться скрыто (в шахтах, штробах и т.д.). Открытая прокладка трубопроводов разрешается в местах подвода воды к водоразборной арматуре, а также в местах, где исключены их механические повреждения.
Прокладывать трубопроводы под перекрытием подвальных помещений следует только в тех случаях, когда предусмотрена защита от механических повреждений.
При горизонтальной прокладке участки водопроводных линий из пластмассовых труб следует прокладывать выше канализационных трубопроводов. При невозможности обеспечить прокладку выше канализационного трубопровода, транспортирующего агрессивные, токсичные, пахучие жидкости, водопровод следует проектировать из труб только со сварными или клеевыми соединениями.
3.4.3. При проектировании трубопроводов следует полностью использовать компенсирующую способность трубопровода. Это достигается путем выбора рациональной схемы прокладки и правильным размещением неподвижных опор, делящих трубопровод на участки, температурная деформация которых происходит независимо один от другого и воспринимается компенсирующими элементами трубопровода.
Размещение опор производят в следующей последовательности:
- на схеме трубопроводов намечают места расположения неподвижных опор с учетом компенсации температурных изменений длины труб элементами трубопровода;
- проверяют расчетом компенсирующую способность участков;
- намечают расположение скользящих и неподвижных опор.
В тех случаях когда температурные изменения длины трубопровода превышают компенсирующую способность его элементов, на нем необходимо установить дополнительный компенсатор, как правило, посередине между неподвижными опорами.
При расстановке опор следует учитывать, что перемещение трубы в плоскости, перпендикулярной оси трубы, ограничивается расстоянием от поверхности до стены.
3.4.4. Запорная и водоразборная арматура должна иметь неподвижное крепление к строительным конструкциям для того, чтобы усилия, возникающие при пользовании арматурой, не передавались на трубы.
Запорную арматуру диаметром до 32 мм с корпусом из полимерных материалов допускается устанавливать без крепления к строительным конструкциям.
3.4.5. Расстояние при параллельной прокладке и между пересекающимися трубопроводами, выполненными из полимерных материалов, и трубопроводами, выполненными из других материалов, в том числе стальными, регламентируется нормативными документами.
3.4.6. Скрытая прокладка в бороздах и штробах должна обеспечивать возможность компенсации деформаций пластмассовых трубопроводов без механических повреждений их элементов.
3.4.7. При сборке фланцевых соединений трубопроводов запрещается устранение перекоса фланцев путем неравномерного натягивания болтов и устранение зазоров между фланцами при помощи клиновых прокладок и шайб.
3.4.8. При скрытой прокладке трубопроводов из полимерных материалов внутренняя поверхность борозд или каналов не должна иметь твердых острых выступов.
3.4.9. При сборке резьбовых соединений должна быть соблюдена соосность металлических и пластмассовых труб и деталей. Поверхность резьбы детали должна быть ровной, чистой и без заусенцев.
3.5. Гидравлический расчет трубопроводов
3.5.1. Величина напора

, необходимая для подачи воды потребителю, определяется по формуле

, (1)
где

- удельные потери напора при температуре воды t, °С (потери напора на единицу длины трубопровода), м/м;
l - длина участка трубопровода, м;

- потери напора в стыковых соединениях и в местных сопротивлениях, м;

- геометрическая высота (отметка самой высокой точки расчетного участка трубопровода), м;

- свободный напор на изливе из трубопровода, м (для санитарно-технических приборов принимается по
приложению 2
СНиП 2.04.01).
Примечание. Допускается

принимать равной 20 - 30%

.
3.5.2. Потери напора на единицу длины трубопровода

без учета гидравлического сопротивления стыковых соединений следует определять по формуле

, (2)
где

- коэффициент гидравлического сопротивления по длине трубопровода;
V - средняя скорость движения воды, м/с;
g - ускорение свободного падения, м/с2;
d - расчетный (внутренний) диаметр трубопровода, м.
Коэффициент гидравлического сопротивления

следует определять по формуле
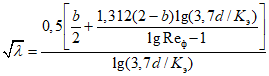
, (3)
где b - число подобия режимов течения воды;

- число Рейнольдса фактическое;

- коэффициент эквивалентной шероховатости, м, приводится в отдельных сводах правил, но не менее 0,00001 м.
Число подобия режимов течения воды b определяют по формуле

, (4)
(при b > 2 следует принимать b = 2). Фактическое число Рейнольдса

определяется по формуле

, (5)
где

- коэффициент кинематической вязкости воды, м2/с.
Число Рейнольдса, соответствующее началу квадратичной области гидравлических сопротивлений при турбулентном движении воды, определяется по формуле

. (6)
3.5.3. Для ориентировочных расчетов по вышеприведенным формулам можно использовать номограммы, приведенные в
Приложении В
.
Номограммы на
рис. В.1
и
В.2
предназначены для определения удельных потерь напора на трение при транспортировании воды с температурой 10 °С.
По номограммам на
рис. В.3
и
В.4
определяется поправочный коэффициент

к величине

, если температура воды отлична от 10 °С.
3.6.1. В местах прохода через строительные конструкции трубы из полимерных материалов необходимо прокладывать в гильзах. Длина гильзы должна превышать толщину строительной конструкции на толщину строительных отделочных материалов, а над поверхностью пола возвышаться на 20 мм. Расположение стыков труб в гильзах не допускается.
3.6.2. Для трубопроводов из полимерных материалов применяются подвижные опоры, допускающие перемещение труб в осевом направлении, и неподвижные опоры, не допускающие таких перемещений.
3.6.3. Неподвижные опоры на трубах следует выполнять с помощью приваренных или приклеенных (в зависимости от материала труб) к телу трубы упорных колец, муфт - для труб диаметром до 160 мм или сегментов - для труб диаметром больше 160 мм.
Примеры расстановки опор приведены на рисунке 1.
Рисунок 1. Примеры расстановки неподвижных опор
Неподвижное крепление трубопровода на опоре путем сжатия трубы не допускается.
В качестве подвижных опор следует применять подвесные опоры или хомуты, выполненные из металла или полимерного материала, внутренний диаметр которых должен быть на 1 - 3 мм (с учетом прокладки и теплового расширения) больше наружного диаметра монтируемого трубопровода.
Между трубопроводом и металлическим хомутом следует помещать прокладку из мягкого материала. Ширина прокладки должна превышать ширину хомута не менее чем на 2 мм.
3.6.4. Расстановку неподвижных опор следует принимать такой, чтобы температурные изменения длины участков трубопроводов не превышали их компенсирующую способность.
3.6.5. При невозможности установки креплений на расчетном расстоянии по конструктивным соображениям трубопроводы допускается прокладывать на сплошном основании.
3.6.6. Длина незакрепленных горизонтальных трубопроводов в местах поворотов и присоединения их к приборам, оборудованию, фланцевым соединениям не должна превышать 0,5 м (рисунок 2).
Рисунок 2. Прокладка трубопроводов в шахтах.
3.6.7. Заделку штроб, коробов, отверстий в междуэтажных перекрытиях и стенах следует выполнять после окончания всех работ по монтажу и испытанию трубопроводов.
3.7. Компенсация температурного удлинения трубопроводов
3.7.1. При проектировании и монтаже трубопроводов из полимерных материалов необходимо учитывать значительные температурные изменения длины и принимать соответствующие меры по их компенсации.
3.7.2. Величину температурного изменения длины трубопровода

определяют по формуле

, (7)
где

- коэффициент теплового линейного расширения материала трубы,

;

- разность между максимальной и минимальной температурами трубопровода;
L - длина трубопровода, м.
3.7.3. Продольные усилия

возникающие в трубопроводе при изменении температуры, без учета компенсации температурных деформаций определяют по формуле

, (8)
где

- модуль упругости материала трубы, МПа;
F - площадь поперечного сечения стенки трубы, м2.
Температурные напряжения необходимо учитывать в любом закрепленном участке трубопровода при любой длине участка.
3.7.4. Основными компенсирующими элементами трубопровода являются отводы, петлеобразные, П-образные, сильфонные и другие виды компенсаторов.
3.7.5. Компенсирующая способность отвода под углом 90° определяется по формуле
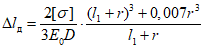
, (9)
где

- максимально допустимое продольное перемещение трубопровода от действия температуры, которое может быть компенсировано отводом, м;

- длина прилегающего к отводу прямого участка трубопровода до подвижной опоры, м;
r - радиус изгиба отвода, м;
D - наружный диаметр труб, м;

- расчетная прочность, МПа;

- модуль упругости, МПа.
Схемы гнутого отвода и компенсатора показаны на рисунке 3.
а - отвод; б - компенсатор
Рисунок 3. Схемы гнутого отвода и компенсатора
3.7.6. Компенсирующая способность П-образного компенсатора определяется по формуле

, (10)
где

- максимально допустимое продольное перемещение трубопровода от действия температуры, которое может быть воспринято компенсатором, м;
h - вылет компенсатора, м;
r - радиус изгиба отводов компенсатора, м;
a - длина прямого участка компенсатора, м;
D - наружный диаметр трубы, м;

- допускаемое напряжение из условий длительной прочности, МПа.
3.7.7. Максимально допустимое расстояние от оси компенсатора до оси неподвижной опоры трубопровода

, см, должно вычисляться по формуле

. (11)
3.7.8. Расстояние l от оси трубы отвода до оси установки скользящей опоры (рисунок 4) следует принимать равным

, (12)
где K - коэффициент, определяемый прочностными и упругими свойствами полимерного материала труб по формуле

, (13)

- расчетная прочность материала трубы, МПа.
а - на отводе; б - на тройниковом ответвлении
Рисунок 4. Схемы расположения опор
3.7.9. В необходимых случаях компенсирующая способность трубопроводов может быть повышена за счет введения дополнительных поворотов, спусков и подъемов.
3.7.10. Компенсация теплового линейного удлинения труб из полимерных материалов может обеспечиваться продольным изгибом при укладке их в виде "змейки" на опоре, ширина которой должна допускать возможность изгиба трубопровода при перепаде температур.
3.7.11. При необходимости увеличения компенсирующей способности Г-, Z- и П-образных элементов трубопроводов применяют метод "растяжки" (предварительное напряжение) при монтаже трубопровода.
3.8. Тепловая изоляция трубопроводов
3.8.1. Трубопроводы для горячей воды (кроме подводок к водоразборным приборам) из полимерных труб должны иметь тепловую изоляцию.
3.8.2. Тепловую изоляцию трубопроводов определяют расчетом согласно
СНиП 2.04.14
. Коэффициент теплопроводности материала должен быть не более 0,05 Вт/(м х °С), но при этом толщина тепловой изоляции должна быть не менее 10 мм.
4. ПРОЕКТИРОВАНИЕ ВНУТРЕННЕЙ КАНАЛИЗАЦИИ И ВОДОСТОКОВ
4.1.1. Системы внутренней канализации зданий следует проектировать из канализационных труб, рассчитанных на транспортирование сточных вод с постоянной температурой не ниже 75 °С и кратковременно не менее 1 мин с температурой не менее 90 °С.
4.1.2. Проектирование системы канализации из труб и соединительных деталей из различных полимерных материалов не допускается.
4.1.3. Системы внутренних водостоков для зданий высотой до 10 м допускается выполнять из безнапорных труб, при большей высоте здания следует применять напорные трубы.
4.1.4. Трубы из полимерных материалов должны быть проложены, как правило, скрыто - в шахтах, коробах, бороздах и т.п.
В местах возможного механического повреждения труб следует применять только скрытую прокладку.
Допускается открытая прокладка канализационных и водосточных трубопроводов в подвалах зданий, не оборудованных под производственные, складские или служебные помещения, на чердаках и в санузлах зданий.
4.1.5. К местам прочистки трубопроводов из полимерных материалов должен быть обеспечен легкий доступ посредством установки дверок, съемных щитов, решеток и т.п.
Диаметры канализационных труб и соединительных деталей должны быть унифицированы по наружному диаметру: 32, 40, 50, 75, 90, 110 и 160 мм. Толщина стенок труб и соединительных деталей зависит от вида полимерного материала и указывается в соответствующих нормативных документах.
4.3. Виды и способы соединения труб
4.3.1. Трубопроводы для систем внутренней канализации соединяются с помощью раструбных соединений с использованием уплотнительных колец, а для труб ПВХ - также на клею.
4.3.2. Фланцевые соединения используются в местах перехода трубопровода на чугунные или стальные трубы или для подключения к оборудованию.
4.3.3. Соединение отводящих трубопроводов со стояками надлежит производить на раструбе с уплотнительным кольцом. При соединении гладких труб между собой допускается применение двухраструбных муфт, при этом муфты необходимо закреплять на опорах.
4.3.4. Гладкие концы чугунных деталей (выпуски трапов, водосточные воронки и т.п.) следует соединять с трубами из полимерных материалов соединительными раструбными патрубками с уплотнительными кольцами или манжетами.
4.3.5. Соединение гладких концов канализационных труб из полимерных материалов с раструбом чугунной канализационной трубы того же диаметра следует производить с применением специальных уплотнительных колец или манжет.
4.4. Прокладка трубопроводов
4.4.1. При прокладке канализационных стояков в коммуникационных шахтах, штробах, каналах и коробах ограждающие конструкции, обеспечивающие доступ в шахту, короб и т.п., должны быть выполнены в соответствии со
СНиП 2.04.01
.
4.4.2. Места прохода стояков через перекрытия допускается заделывать цементным раствором на всю толщину перекрытия.
При прокладке труб в перекрытии их следует обертывать гидроизоляционным материалом без зазора.
4.4.3. Трубопроводы не должны примыкать вплотную к поверхности строительных конструкций. Расстояние в свету между трубами и строительными конструкциями должно быть не менее 20 мм.
4.4.4. Компенсация температурного удлинения трубопроводов при использовании сварных и клеевых соединений должна обеспечиваться с помощью раструбных соединений с уплотнительными кольцами, вставляемыми в обычный или компенсационный (удлиненный) раструб.
4.4.5. Следует предусматривать жесткое и прочное крепление санитарных приборов к строительным конструкциям без передачи усилий на трубопроводы.
4.5. Гидравлический расчет трубопроводов
4.5.1. Диаметр канализационного стояка рассчитывается на пропуск расчетного расхода воды из условия устойчивости против срыва гидравлических затворов санитарно-технических приборов, присоединенных к этому стояку. При этом величина разрежения, возникающего в стояке, не должна превышать минимальной высоты гидравлических затворов.
Все отводные канализационные трубопроводы, как правило, следует рассчитывать так, чтобы при расчетном расходе стоков они работали в безнапорном режиме.
Водосточные стояки и соединения должны быть герметичными при давлении воды, равном высоте стояка, и прочными при засорении и переполнении.
4.5.2. Допустимая величина разрежения в вентилируемых и невентилируемых канализационных стояках не должна превышать

, где

- высота наименьшего из гидравлических затворов санитарно-технических приборов, присоединенных к канализационному стояку.
4.5.3. Величину разрежения в вентилируемом канализационном стояке следует определять по формуле
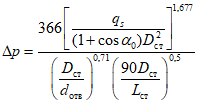
, (14)
где

- величина разрежения в стояке, мм вод. ст.;

- расчетный расход стоков, м3/с;

- угол присоединения поэтажного отвода к стояку, град.;

- диаметр стояка (внутренний), м;

- диаметр поэтажного отвода, м;

- рабочая высота стояка, м.
Примечание. При 90

>

следует принимать 90

=

.
4.5.4. Величину разрежения в невентилируемом канализационном стояке следует определять по формуле

, (15)
где

- скорость водовоздушной смеси, м/с, которую определяют по формуле

, (16)
где

- расход воздуха, эжектируемого (увлекаемого) в стояк движущимися в нем сверху вниз стоками, м3/с, определяется по формуле
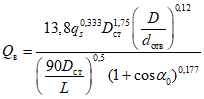
, (17)

- площадь сечения стояка, м2.
Примечание. См. примечание к 4.5.3.
4.5.5. Уклон самотечного трубопровода

следует определять по формуле

, (18)
где

- коэффициент гидравлического сопротивления трубопровода (канала);
V - средняя скорость течения жидкости, м/с;
g - ускорение свободного падения, м/с2;

- гидравлический радиус потока, м;

- безразмерный показатель степени, характеризующий режим турбулентного течения жидкости - переходный (

< 2) или квадратичный (

= 2).
При

> 2 следует принимать

= 2.
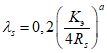
, (19)
где a - эмпирический показатель степени, зависящий от
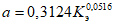
; (20)
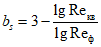
. (21)
Число Рейнольдса

определяют по формуле
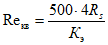
. (22)
Число Рейнольдса

определяют по формуле

, (23)
где

- коэффициент кинематической вязкости жидкости, м2/с. Для бытовых стоков следует принимать

=

м2/с.
Примечание. Средняя скорость течения жидкости

при неполном наполнении трубопровода (канала) равна:
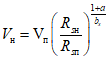
, (24)
где

- средняя скорость течения жидкости при полном наполнении трубопровода, м/с;

,

- гидравлические радиусы при неполном и полном наполнении трубопровода, м.
4.5.6. Расход жидкости

равен:

, (25)
где

- живое сечение потока жидкости при данном наполнении трубопровода, м2, которое равно:

.
Значения

,

,

,

представлены в таблице 2.
Таблица 2
Наполнение трубопровода
|
Значение гидравлического радиуса
|
Отношение гидравлических радиусов
|
|
0,1
|
0,0635
|
0,2540
|
0,0409
|
0,2
|
0,1206
|
0,4824
|
0,1118
|
0,3
|
0,1709
|
0,6836
|
0,1982
|
0,4
|
0,2142
|
0,8568
|
0,2934
|
0,5
|
0,2500
|
1,0000
|
0,3927
|
0,6
|
0,2776
|
1,1104
|
0,4920
|
0,7
|
0,2962
|
1,1848
|
0,5872
|
0,8
|
0,3042
|
1,2168
|
0,6736
|
0,9
|
0,2980
|
1,1920
|
0,7445
|
1,0
|
0,2500
|
1,0000
|
0,7854
|
4.5.7. Диаметр безнапорного трубопровода в зависимости от его наполнения и расхода сточной жидкости допускается определять по номограмме
Приложения Г
.
4.6.1. Крепить трубопроводы канализации и внутренних водостоков необходимо в местах, указанных в проекте, соблюдая следующие требования:
- крепления должны направлять усилия, возникающие при удлинении трубопровода, в сторону соединений, используемых в качестве компенсаторов;
- крепления следует устанавливать у раструбов трубопроводов;
- крепления должны обеспечить уклон и соосность деталей трубопроводов;
- установленные на гладком конце трубы крепления должны допускать расчетные температурные удлинения трубопровода;
- расстояние между креплениями для трубопроводов диаметром до 50 и до 110 мм с соединениями на кольцах должно приниматься в зависимости от материала трубы по соответствующему своду правил;
- при установке креплений на соединительных деталях необходимо предусматривать расстояние для компенсации температурного удлинения. При невозможности установки креплений на соединительной детали соседние детали закрепляют хомутами на расстояниях, обеспечивающих удлинение соединительной детали.
4.6.2. Вертикальные участки трубопровода должны иметь крепления, устанавливаемые: под раструбом; на патрубках, используемых для присоединения к сети унитазов и трапов. На отводных трубах от гидрозатворов крепления не устанавливают.
4.6.3. Перед прокладкой трубопроводов и расстановкой креплений следует прочно закрепить к строительным конструкциям санитарные приборы, водосточные воронки и другие приемники сточных вод. Металлические соединительные детали должны иметь самостоятельные крепления, предотвращающие передачу нагрузок на трубы.
4.6.4. При сборке фланцевых соединений трубопроводов запрещается устранение перекоса фланцев путем неравномерного натягивания болтов и устранение зазоров между фланцами при помощи клиновых прокладок и шайб.
4.6.5. При скрытой прокладке трубопроводов из полимерных материалов внутренняя поверхность борозд или каналов не должна иметь твердых острых выступов.
4.6.6. При сборке резьбовых соединений должна быть соблюдена соосность металлических и пластмассовых деталей. Поверхность резьбы детали должна быть ровной, чистой и без заусенцев.
5. ПРОЕКТИРОВАНИЕ НАРУЖНОГО ВОДОПРОВОДА
5.1.1. Выбор напорных труб из полимерных материалов для наружных систем водоснабжения производится с учетом климатических условий и технико-экономических оценок.
5.1.2. Трубы подбирают расчетом, при этом для наружного водопровода, как правило, следует принимать трубы типа "С" (PN-6) и выше.
5.2.1. Требования к геометрическим размерам труб и их параметрам указаны в
разделе 3.2
.
5.2.2. Длину отрезков труб или бухты указывают в документации изготовителя.
5.3.1. Для соединения труб из полимерных материалов должны использоваться, как правило, соединительные детали из полимерных материалов. Допускается использовать специальные соединительные детали из металла.
5.3.2. Для соединения труб диаметром до 110 мм из полиолефинов следует использовать сварку. Трубы из ПВХ, стеклопластиков и базальтопластиков следует соединять на раструбных соединениях, уплотняемых профильным резиновым кольцом, или на клею.
5.3.3. Для присоединения труб из полимерных материалов к арматуре и металлическим трубам следует использовать пластмассовые буртовые втулки и свободные металлические фланцы или неразъемные соединения из пластмассы-металла.
5.4. Прокладка трубопроводов
5.4.1. Трассировка водопровода должна осуществляться в соответствии со
СНиП 2.04.02
с учетом способа прокладки - в грунте, в коллекторах, непроходных каналах либо в реконструируемых трубопроводах, определяемого местными условиями и результатами экономического расчета.
5.4.2. При новом строительстве предпочтение следует отдавать прокладке трубопровода в грунте.
5.4.3. Следует использовать возможность поворота трассы за счет изгиба трубы с минимальным радиусом

, (26)
где

- модуль упругости полимера при растяжении, МПа;
D - наружный диаметр труб, мм;

- расчетная прочность (предел текучести) для материала труб при растяжении, МПа.
5.4.4. Поворот трассы может быть осуществлен также за счет отклонения оси одной трубы относительно другой в раструбном соединении, уплотняемом кольцом, на угол до 2°.
5.4.5. Минимальное заглубление водопровода до верха трубопровода согласно
СНиП 2.04.02
должно превышать глубину промерзания грунта для данной местности не менее чем на 0,5 м. Уменьшать глубину заложения трубопровода допускается только при применении тепловой изоляции, конструкция которой не поглощает влагу.
5.4.6. Минимальное заглубление водопровода из условий прочности при отсутствии транспортных нагрузок (кроме поливочного водопровода) должно быть не менее 1,0 м.
5.4.7. Пересечение водопровода с другими коммуникациями, а также автомобильными и железными дорогами следует выполнять в соответствии с требованиями
СНиП 2.04.02
.
5.4.8. При пересечении с канализацией на расстоянии, меньшем 0,4 м (по вертикали в свету), водопроводы из полимерных труб должны проектироваться в футлярах. Расстояние от края футляра до пересекаемого трубопровода должно быть не менее 5 м в каждую сторону.
5.4.9. Соединение пластмассовых труб с трубами из других материалов (стальными, чугунными, асбестоцементными и т.д.) следует выполнять на разъемных соединениях. При подземной прокладке такие соединения следует устанавливать в колодцах.
5.4.10. Пересечение пластмассовым трубопроводом стен сооружений следует предусматривать в футлярах. Зазор между футляром и трубопроводом заделывается эластичными материалами, предотвращающими попадание влаги внутрь футляра.
5.4.11. При прокладке труб в тоннелях (коммуникационных коллекторах) следует выполнять требования
СНиП 2.07.01
, при этом электрические кабели и провода должны прокладываться выше трубопроводов из полимерных материалов и должны быть конструктивно выделены.
5.4.12. Крепление арматуры к стенкам и днищу колодца, туннеля или канала следует производить с помощью анкерных болтов и хомутов или замоноличивать бетоном.
5.4.13. Пересечение трубопроводом стенок колодцев или фундаментов зданий следует предусматривать в стальных или пластмассовых футлярах. Зазор между футляром и трубопроводом заделывается водонепроницаемым эластичным материалом.
5.5. Расчет трубопровода на прочность
Расчет трубопровода на прочность возможно производить по различным методикам, приведенным в справочной литературе. Одна из них дана в
Приложении Д
.
5.6. Гидравлический расчет трубопровода
Гидравлический расчет систем водоснабжения, изложенный в
разделе 3.5
, следует применять также и для расчета наружных систем водоснабжения.
5.7. Компенсация температурного удлинения
5.7.1. Компенсация температурного удлинения подземных водопроводов холодной воды из труб с раструбными соединениями, уплотняемыми резиновыми кольцами, достигается в раструбах.
5.7.2. Для подземных водопроводов на сварных или других неразъемных соединениях, прокладываемых в грунте, с учетом защемления труб грунтом специальной компенсации не требуется. При прокладке в каналах следует проводить расчет на компенсацию удлинения в соответствии с
разделом 3.7
.
6. ПРОЕКТИРОВАНИЕ НАРУЖНОЙ КАНАЛИЗАЦИИ, ВОДОСТОКОВ И ДРЕНАЖЕЙ
6.1.1. Выбор труб следует производить с учетом состава стоков, их температуры, на основании гидравлических и прочностных расчетов.
6.1.2. Для самотечной канализации следует использовать трубы канализационного сортамента. Применение напорных труб должно быть обосновано.
6.2.1. Для безнапорной канализации гладкие трубы унифицированы по наружным диаметрам, кроме труб из стекло- и базальтопластиков, изготавливаемых намоткой.
Трубы по кольцевой жесткости оболочки подразделяются на классы: нежесткая, полужесткая и жесткая. Класс труб приведен в
Приложении А
.
6.3.1. На трубопроводах самотечной канализации следует предусматривать как разъемные, так и неразъемные соединения.
6.3.2. В качестве разъемных следует использовать раструбные соединения, уплотняемые кольцами различного профиля.
6.3.3. Основные виды и способы соединений труб приведены в
разделе 3.3
.
6.3.4. Для напорных трубопроводов канализации следует использовать преимущественно неразъемные соединения - склеивание и сварку.
6.3.5. Разъемные соединения (фланцевые и др.) на напорной канализации, как правило, используются для соединения труб с оборудованием.
6.4. Прокладка трубопроводов
6.4.1. Трассировка наружной канализации должна выполняться с учетом требований
СНиП 2.04.03
.
6.4.2. Трубопроводы самотечной канализации должны быть только прямолинейными. Изменение диаметра трубопровода и его направления допускается только в колодцах.
Напорные системы канализации выполняют согласно
разделу 5
.
6.5. Расчет трубопровода на прочность
Расчет самотечных трубопроводов на прочность следует производить по методике, приведенной в
Приложении Д
.
6.6. Гидравлический расчет трубопровода
Гидравлический расчет самотечных подземных трубопроводов канализации производят по формулам, приведенным в
разделе 4.5
.
6.7. Компенсация температурного удлинения труб
6.7.1. Необходимость компенсации температурного удлинения труб в напорной канализации устанавливается расчетом в соответствии с
разделом 3.7
настоящего Свода правил с учетом защемляющего действия грунта.
При защемлении трубопровода грунтом удлинение трубопровода уменьшается. Величина уменьшения

определяется по формуле

, (27)
где

- коэффициент трения материала о грунт, определяемый опытным путем; при отсутствии данных может быть ориентировочно принят равным 0,4;

- объемный вес грунта, Н/м3;
H - глубина заложения трубопровода, м;
L - длина трубопровода, м;

- модуль упругости материала в направлении деформации, Па;
s - толщина стенки трубопровода, м;

- коэффициент уплотнения грунта, принимается равным 1 при степени уплотнения 0,95 и 0,5 - при неконтролируемой степени уплотнения при засыпке траншеи.
6.7.2. Компенсация температурных деформаций трубопроводов в самотечной канализации обеспечивается:
- раструбными соединениями, уплотняемыми кольцами;
- частично в канализационных колодцах путем устройства прохода через стенки колодца и набивки лотка.
6.8. Колодцы для систем канализации
6.8.1. Для систем водоотведения допускается применять канализационные, водосточные и водоприемные колодцы из: полимерных материалов (ПЭ, ПВХ и др.), комбинированные (элементы из полимерных материалов в сочетании с элементами из железобетона), железобетонные и кирпичные. Размеры колодцев должны соответствовать указанным в
СНиП 2.04.03
.
6.8.2. Колодцы из полимерных материалов следует применять совместно с защитной плитой из железобетона и традиционными элементами люка из металла.
6.8.3. Лотковая часть колодцев из полимерных материалов должна иметь готовые лотки из полимерных материалов, а также выступающие патрубки для присоединения трубопровода.
7.1.1. При строительстве трубопроводов с применением труб из полимерных материалов для обеспечения требуемого качества строительства необходимо производить:
- проверку квалификации монтажников и сварщиков;
- входной контроль качества применяемых труб, соединительных деталей и арматуры;
- технический осмотр сварочных устройств и применяемого инструмента;
- систематический операционный контроль качества сборки и режимов сварки;
- визуальный контроль качества сварных соединений и контроль их геометрических параметров;
- механические испытания сварных и других соединений.
7.1.2. Контроль качества сварных и соединительных деталей, входной контроль труб и т.д. следует производить в соответствии с требованиями, указанными в
разделе 7.2
.
7.2. Входной контроль качества труб и соединительных деталей
7.2.1. Входной контроль качества труб и соединительных деталей осуществляется строительно-монтажной организацией, допущенной к выполнению работ по монтажу трубопроводов из полимерных материалов.
7.2.2. Входной контроль включает следующие операции:
- проверка целостности упаковки;
- проверка маркировки труб и соединительных деталей на соответствие технической документации;
- внешний осмотр наружной поверхности труб и соединительных деталей, а также внутренней поверхности соединительных деталей;
- измерение и сопоставление наружных и внутренних диаметров и толщины стенок труб с требуемыми. Измерения следует производить не менее чем по двум взаимно перпендикулярным диаметрам. Результаты измерений должны соответствовать величинам, указанным в технической документации на трубы и соединительные детали. Овальность концов труб и соединительных деталей, выходящая за пределы допускаемых отклонений, не разрешается.
7.2.3. Все трубы и соединительные детали зарубежной поставки должны иметь техническое свидетельство.
7.2.4. Не допускается использовать для строительства трубы и соединительные детали с технологическими дефектами, царапинами и отклонениями от допусков больше, чем предусмотрено стандартом или техническими условиями.
Результаты входного контроля оформляются актом по форме, приведенной в
Приложении Е
.
7.3. Сварка и склеивание труб из полимерных материалов
7.3.1. Соединения труб и деталей из свариваемых полимерных материалов должны выполняться при помощи сварки контактным нагревом (стыковой, раструбной) либо соединительными деталями с закладным нагревательным элементом.
7.3.2. Стыковая сварка рекомендуется для соединения между собой труб и соединительных деталей наружным диаметром более 50 мм и толщиной стенки более 4 мм (рисунок 5).
а - центровка и закрепление в зажимах сварочной машины концов
свариваемых труб; б - механическая обработка торцов труб
с помощью торцовки (1); в - проверка точности совпадения
торцов по величине зазора (с);
г - нагрев и оплавление свариваемых поверхностей
нагретым инструментом (2); д - осадка стыка
Рисунок 5. Последовательность процесса сборки
и стыковой сварки труб контактным нагревом
Раструбная сварка рекомендуется для труб наружным диаметром до 110 мм и стенками любой толщины.
При сварке необходимо подбирать трубы и соединительные детали по партиям поставки. Не допускается сварка труб и деталей из различных полимерных материалов.
При стыковой сварке максимальная величина несовпадения кромок не должна превышать 10% номинальной толщины стенки трубы.
Внутренний диаметр раструба соединительных деталей должен быть меньше номинального наружного диаметра свариваемой трубы в пределах допуска.
7.3.3. При стыковой сварке непосредственно перед нагревом свариваемые поверхности должны подвергаться механической обработке для снятия возможных загрязнений и окисной пленки. После механической обработки между торцами труб, приведенными в соприкосновение с помощью центрирующего приспособления, не должно быть зазоров, превышающих 0,5 мм для труб диаметром до 110 мм и 0,7 мм - для больших диаметров.
Концы труб при раструбной сварке должны иметь наружную фаску под углом 45° на 1/3 толщины стенки трубы.
7.3.4. Сварку труб встык в монтажных условиях следует производить на сварочных установках, обеспечивающих автоматизацию основных процессов сварки и компьютерный контроль с регистрацией технологического процесса (см.
рисунок 5
).
Для предотвращения налипания расплавленного материала при сварке труб нагреватель следует покрыть теплостойким антиадгезионным покрытием.
7.3.5. При контактной стыковой сварке с применением сварочных машин и монтажных приспособлений следует выполнять следующие операции:
- установка и центровка труб в зажимном центрирующем приспособлении;
- механическая торцовка труб и обезжиривание торцов;
- нагрев и оплавление свариваемых поверхностей под давлением;
- удаление сварочного нагревателя;
- сопряжение разогретых свариваемых поверхностей (осадка) под давлением;
- охлаждение сварного шва под давлением.
7.3.6. Основными контролируемыми параметрами процесса стыковой сварки являются: температура рабочих поверхностей нагревателя, продолжительность нагрева, глубина оплавления, величина контактных давлений при оплавлении и осадке. Высота h внутреннего и наружного грата (валиков) после сварки должна быть не более 2 - 2,5 мм при толщине стенки трубы s до 5 мм и не более 3 - 5 мм при толщине стенок 6 - 20 мм.
7.3.7. Контактная раструбная сварка включает в себя следующие операции:
- нанесение метки на расстоянии от торца трубы, равном глубине раструба соединительной детали плюс 2 мм;
- установку раструба на дорне;
- установку гладкого конца трубы в гильзе нагревательного элемента;
- нагрев в течение заданного времени свариваемых деталей;
- одновременное снятие деталей с дорна и гильзы;
- соединение деталей между собой до метки с выдержкой до отвердения оплавленного материала.
При сварке поворот деталей относительно друг друга после сопряжения деталей не допускается. После каждой сварки необходима очистка рабочих поверхностей от налипшего материала. Время выдержки свариваемых изделий до частичного отвердения зависит от применяемого материала.
7.3.8. Маркировку сварных стыков производят сразу после окончания операции на горячем расплаве наружного грата в двух диаметрально противоположных точках в процессе охлаждения стыка в зажимах центратора сварочной установки или монтажного приспособления.
Для маркировки стыков рекомендуется использовать клейма типа ПУ-6 или ПУ-8 по
ГОСТ 2930
.
7.3.9. Сварку при помощи соединительных деталей с закладными электронагревательными элементами применяют для соединения пластмассовых труб диаметром от 20 до 500 мм с любой толщиной стенки, а также для приварки к трубопроводу седловых отводов.
Сварку муфтами с закладными нагревателями рекомендуется производить для:
- соединения длинномерных труб;
- соединения труб с толщиной стенки менее 5 мм;
- ремонта трубопровода в стесненных условиях.
Сварку трубопроводов с применением соединительных деталей с закладными нагревателями производят при температуре окружающего воздуха не ниже минус 5 °С и не выше +35 °С.
В случаях необходимости проведения сварки при других температурах воздуха работы выполняют в укрытиях (палатки, шатры и т.п.) с обеспечением подогрева зоны сварки. Место сварки защищают от воздействия влаги, песка, пыли и т.п.
7.3.10. Технологический процесс соединения труб с помощью муфт с закладными нагревателями включает:
- подготовку концов труб - очистка от загрязнения, разметка, механическая обработка (циклевка) свариваемых поверхностей и обезжиривание их. Общая длина очищаемых концов труб должна быть не меньше 1,5 длины применяемых для сварки муфт;
- сборку стыка (установка и закрепление концов свариваемых труб в зажимах центрирующего приспособления с одновременной посадкой муфты);
- подключение к сварочному аппарату;
- сварку (задание программы процесса сварки, нагрев, охлаждение соединения) по рисунку 6.
1 - труба; 2 - метка посадки муфты и механической обработки
поверхности трубы; 3 - муфта; 4 - закладной нагреватель;
5 - токоподводящие (сварочные) провода
Рисунок 6. Сварка труб муфтой с закладным нагревателем
Перед механической обработкой на концы свариваемых труб на длину 1/2 длины муфты наносят метки глубины посадки муфты для обозначения зоны обработки.
Механическая обработка концов труб заключается в снятии с поверхности размеченного конца трубы слоя материала толщиной 0,1 - 0,2 мм, а также удалении заусенцев. Зазор между свариваемыми поверхностями трубы и раструбной детали не должен превышать 0,3 мм.
Свариваемые поверхности труб после механической обработки и муфты тщательно обезжиривают путем протирки специально рекомендованными для этих целей составами.
Муфты с закладными нагревателями, поставляемые изготовителем в индивидуальной герметичной упаковке, вскрываемой непосредственно перед сборкой, обезжириванию не подвергают.
7.3.11. Допуск перпендикулярности торцов труб и максимальный зазор между ними приведены в
таблицах 3
и
4
(рисунок 7).
Рисунок 7. Установка зазора при стыковке труб
Таблица 3
Допуск перпендикулярности торцов труб
В миллиметрах
┌─────────────────┬────┬─────┬─────┬───┬────┬────┬─────┬───┬─────┐
│Наружный диаметр │ 20 │ 32 │ 40 │63 │ 90 │110 │ 125 │160│ 200 │
├─────────────────┼────┼─────┼─────┼───┼────┼────┼─────┼───┼─────┤
│a │2 │2 │2 │3 │4 │5 │6 │7 │8 │
└─────────────────┴────┴─────┴─────┴───┴────┴────┴─────┴───┴─────┘
Таблица 4
Максимальный допустимый зазор между двумя трубами
В миллиметрах
┌────────────────────┬────┬────┬───┬────┬────┬────┬────┬────┬────┐
│Наружный диаметр │ 20 │ 32 │40 │ 63 │ 90 │110 │125 │160 │200 │
├────────────────────┼────┼────┼───┼────┼────┼────┼────┼────┼────┤
│e │<*> │<*> │<*>│7 │9 │11 │13 │16 │20 │
├────────────────────┴────┴────┴───┴────┴────┴────┴────┴────┴────┤
│ <*> Во внутренней полости муфт диаметрами 20, 32, 40 мм│
│предусмотрен технологический центральный буртик для упора концов│
│свариваемых труб. │
└────────────────────────────────────────────────────────────────┘
7.3.12. Процесс сборки включает:
- надевание муфты на конец первой трубы до совмещения торцов муфты и трубы, закрепление конца трубы в зажиме монтажного приспособления;
- установку в упор в торец первой трубы конца второй трубы и закрепление в зажиме монтажного приспособления;
- надвижение муфты на конец второй трубы на 1/2 длины муфты до упора в зажиме приспособления или до метки, нанесенной на трубу;
- подключение к клеммам муфты токоподводящих проводов от сварочного аппарата.
Во избежание повреждения закладных нагревателей (проволочных электроспиралей) надевание муфты на конец трубы или введение конца трубы в муфту производят с осторожностью без больших усилий, перекосов и прокручивания.
Собранные трубы укладывают прямолинейно без изгиба и провисания, клеммы токоподвода муфты располагают с возможностью свободного обслуживания. Параметры режимов сварки устанавливают на сварочном аппарате в зависимости от сортамента муфты или считывают со штрихового кода с муфты или магнитной карточки при помощи датчика в зависимости от вида используемых муфт и сварочных аппаратов. После включения аппарата процесс сварки проходит в автоматическом режиме.
После завершения нагрева сварное соединение можно перемещать не ранее, чем через 20 мин охлаждения.
7.3.13. Приварку к трубам седловых отводов (
рисунок 8
) производят в следующей последовательности:
- размечают место приварки отвода на трубе;
- поверхность трубы в месте приварки отвода зачищают, а затем обезжиривают;
- привариваемую поверхность отвода, если он поставляется изготовителем в герметичной индивидуальной упаковке, вскрываемой непосредственно перед сборкой, обезжириванию не подвергают;
- отвод устанавливают на трубу и прикрепляют к ней с помощью механического зажима;
- подключают к контактным клеммам токопровода сварочные провода и производят сварку.
а - отвод с седловым нагревателем; б - отвод с кольцевым
нагревателем; 1 - труба; 2 - метки посадки отводов и
механической обработки поверхности трубы; 3 - отвод;
4 - закладной нагреватель; 5 - полухомут;
6 - винты крепления; F - направление усилия
сжатия отвода при сборке и сварке
Рисунок 8. Сварка седловых отводов с закладными
нагревателями с трубой
После охлаждения через патрубок приваренного отвода производят сверловку (фрезерование) стенки трубы для соединения внутренних полостей отвода и трубы.
7.3.14. Контроль качества сварных соединений выполняется в соответствии с нормативной документацией. Для оценки качества сварных соединений, выполненных при помощи муфт и отводов с закладными нагревателями, муфтовые соединения испытываются на сплющивание, а седловые отводы - на разрыв.
7.3.15. Трубы из несварных полимерных материалов, в том числе стекло- и базальтопластиковые, склеиваются между собой и с фасонными частями внахлест.
7.3.16. Склеиваемые поверхности должны проходить специальную механическую обработку, обезжириваться, покрываться клеем.
7.3.17. Состав клея или его марка должны соответствовать материалу трубопровода.
7.3.18. Конфигурация и размеры клеевых соединений должны выполняться по специальным регламентам с учетом используемых труб, срока службы и технологии выполнения монтажных работ.
7.3.19. В регламенте должна указываться технология склеивания, включающая технологические процессы подготовки поверхности, а при необходимости приготовление самого клея, собственно самого процесса склеивания, время до испытания соединения с указанием необходимых параметров.
7.4. Соединение труб на металлических соединительных деталях
Трубы из полимерных материалов, не соединяющиеся с помощью сварки или склеивания, следует соединять между собой и с соединительными деталями с помощью металлических резьбовых соединений с обжимными кольцами, муфтами или на накидных гайках.
7.5. Монтаж внутренних сетей водопровода
7.5.1. Монтаж внутренних систем водоснабжения следует производить в соответствии с проектом производства работ и технологических карт, при положительной температуре с соблюдением требований
СНиП 3.05.01
.
7.5.2. Монтаж трубопроводов следует выполнять после окончания газо- и электросварочных работ.
7.5.3. При монтаже следует применять, как правило, укрупненные узлы трубопроводов.
7.5.4. Резьбовые соединения труб и соединительных деталей следует выполнять вручную или с использованием ключей с регулируемым моментом.
7.6. Монтаж внутренней канализации и водостоков
7.6.1. Монтаж внутренних сетей канализации и водостоков может выполняться как с использованием отдельных труб и соединительных деталей с креплением их по месту, так и с использованием укрупненных узлов, в том числе и смонтированных в санитарно-технических кабинах, с сопряжением стояков кабин межэтажными вставками. Монтаж трубопроводов следует вести по схеме "снизу вверх".
7.6.2. При сборке раструбных соединений с уплотнительными кольцами выполняются следующие операции:
- очистка от загрязнения наружной поверхности гладкого конца детали или трубы и внутренней поверхности раструба;
- очистка уплотнительного кольца от грязи и масел;
- укладка уплотнительного кольца в желобок раструба;
- смазка гладкого конца трубы или соединительной детали и уплотнительного кольца мыльным раствором, глицерином или их смесью (применять для смазки солидол или другие аналогичные смазки запрещается);
- введение гладкого конца в раструб до метки с обязательной проверкой качества сборки путем собранных деталей относительно друг друга на угол до 45° с возвращением в монтажное положение вручную.
7.6.3. Закрепление хомутов опор на стояках и отводящих трубопроводах следует производить после соединения их с санитарными приборами в проектном положении.
7.7. Монтаж подземных сетей водоснабжения и канализации из полимерных труб
7.7.1. Прокладку сетей водоснабжения и канализации следует выполнять в соответствии с требованиями
СНиП 3.01.01
.
7.7.2. Ширина траншеи по дну должна быть не менее чем на 40 см больше наружного диаметра трубопровода. При плотных и твердых грунтах на дне траншеи перед укладкой труб следует предусматривать постель из песка толщиной не менее 10 см.
При укладке длинномерных труб и рытье траншей узкозахватным цепным экскаватором ширина траншеи может быть уменьшена.
7.7.3. Монтаж трубопроводов следует выполнять: с раструбными соединениями на дне траншеи; с неразъемными соединениями, как правило, на бровке траншеи.
7.7.4. При засыпке трубопроводов над верхом трубы обязательно устройство защитного слоя из песчаного или мягкого местного грунта толщиной не менее 30 см, не содержащего твердых включений (щебня, камней, кирпичей и т.д.). Подбивка грунтом трубопровода производится ручным немеханизированным инструментом. Уплотнение грунта в пазухах между стенкой траншеи и трубой, а также всего защитного слоя следует проводить ручной механической трамбовкой до достижения коэффициента уплотнения, установленного проектом. Уплотнение первого защитного слоя толщиной 10 см непосредственно над трубопроводом производят ручным инструментом.
7.7.5. Раструбные соединения напорных труб выполняют по следующей технологии: очистка от грязи и масел гладкого конца трубы; нанесение на гладком конце трубы метки, обозначающей глубину надвигания конца трубы в раструб; помещение уплотнительного кольца в паз раструба; смазка гладкого конца трубы и уплотнительного кольца (глицериновый или мыльный раствор); надвигание гладкого конца трубы в раструб до метки. На концах труб должна быть фаска под углом 15°, выполненная в заводских условиях или на месте монтажа. Сборку раструбных соединений диаметром до 110 мм осуществляют вручную, для труб большего диаметра используют натяжные монтажные приспособления. Правильность сборки соединения и установки уплотнительного кольца проверяется щупом толщиной 0,5 мм.
7.7.6. Сборку раструбных соединений следует производить при температуре наружного воздуха не ниже нуля. Уплотнительные кольца до начала монтажа должны находиться в теплом помещении.
7.7.7. При засыпке пазух и устройстве защитного слоя грунта соединения трубопроводов оставляют незасыпанными до проведения предварительных испытаний на герметичность. Засыпку пазух и уплотнение грунта в приямках производят с использованием механических трамбовок.
7.7.8. Монтаж узлов в колодцах производят одновременно с прокладкой трубопровода. Присоединение трубопроводов к фланцам, запорной и регулирующей арматуре производят перед засыпкой трубопровода защитным слоем грунта, без затяжки болтов. Окончательная затяжка болтовых соединений выполняется непосредственно перед гидравлическим испытанием системы.
8. ИСПЫТАНИЕ И СДАЧА ТРУБОПРОВОДОВ В ЭКСПЛУАТАЦИЮ
8.1. Согласно
СНиП 3.05.04
напорные и безнапорные трубопроводы водоснабжения и канализации испытывают на прочность и плотность (герметичность) гидравлическим или пневматическим способом дважды (предварительное и окончательное).
8.2. Предварительное испытательное (избыточное) гидравлическое давление при испытании на прочность, выполняемое до засыпки траншеи и установки арматуры (гидрантов, предохранительных клапанов, вантузов), должно быть равно расчетному рабочему давлению, умноженному на коэффициент 1,5.
8.3. Окончательное испытательное гидравлическое давление при испытаниях на плотность, выполняемых после засыпки траншеи и завершения всех работ на данном участке трубопровода, но до установки гидрантов, предохранительных клапанов и вантузов, вместо которых на время испытания устанавливают заглушки, должно быть равно расчетному рабочему давлению, умноженному на коэффициент 1,3.
8.4. До проведения испытания напорных трубопроводов с раструбными соединениями с уплотнительными кольцами по торцам трубопровода и на отводах необходимо устраивать временные или постоянные упоры.
8.5. Предварительное гидравлическое испытание напорных трубопроводов следует производить в следующем порядке:
- трубопровод заполнить водой и выдержать без давления в течение 2 ч;
- в трубопроводе создать испытательное давление и поддерживать его в течение 0,5 ч;
- испытательное давление снизить до расчетного и произвести осмотр трубопровода.
Выдержка трубопровода под рабочим давлением производится не менее 0,5 ч. Ввиду деформации оболочки трубопровода необходимо поддерживать в трубопроводе испытательное или рабочее давление подкачкой воды до полной стабилизации.
Трубопровод считается выдержавшим предварительное гидравлическое испытание, если под испытательным давлением не обнаружено разрывов труб или стыков и соединительных деталей, а под рабочим давлением не обнаружено видимых утечек воды.
8.6. Окончательное гидравлическое испытание на плотность проводится в следующем порядке:
- в трубопроводе следует создать давление, равное расчетному рабочему давлению, и поддерживать его 2 ч; при падении давления на 0,02 МПа производится подкачка воды;
- давление поднимают до уровня испытательного за период не более 10 мин и поддерживают его в течение 2 ч.
Трубопровод считается выдержавшим окончательное гидравлическое испытание, если фактическая утечка воды из трубопровода при испытательном давлении не превышает значений, указанных в таблице 5.
Таблица 5
Допустимая утечка воды на участке трубопровода длиной 1 км
при окончательных испытаниях на герметичность
Наружный диаметр труб, мм
|
Допустимая утечка, л/мин, для труб
|
с неразъемными (сварными, клеевыми) соединениями
|
с раструбными соединениями на уплотнительных кольцах
|
63 - 75
|
0,2 - 0,24
|
0,3 - 0,5
|
90 - 110
|
0,26 - 0,28
|
0,6 - 0,7
|
125 - 140
|
0,35 - 0,38
|
0,9 - 0,95
|
160 - 180
|
0,42 - 0,6
|
1,05 - 1,2
|
200
|
0,56
|
1,4
|
250
|
0,7
|
1,55
|
280
|
0,8
|
1,6
|
315
|
0,85
|
1,7
|
355
|
0,9
|
1,8
|
400 - 450
|
1,1 - 0,5
|
1,95 - 2,1
|
500 - 560
|
1,1 - 1,15
|
2,2 - 2,3
|
630
|
1,2
|
2,4
|
710
|
1,3
|
2,55
|
800
|
1,35
|
2,70
|
900
|
1,45
|
2,90
|
1000
|
1,5
|
3,0
|
1200
|
1,6
|
3,0
|
8.7. Гидравлические испытания самотечных канализационных сетей выполняют после завершения гидроизоляционных работ в колодцах в два этапа: без колодцев (предварительное) и совместно с колодцами (окончательное).
8.8. Окончательное испытание трубопровода канализации совместно с колодцами производят согласно
СНиП 3.05.04
.
8.9. Гидравлические испытания систем из полимерных материалов внутренних трубопроводов проводят при положительной температуре окружающей среды не ранее, чем через 24 ч после выполнения последнего сварного и клеевого соединения.
8.10. Гидравлические испытания систем внутренних водостоков осуществляют путем заполнения их водой на всю высоту стояков. Испытания проводят после наружного осмотра трубопроводов и устранения видимых дефектов. Гидравлическое испытание склеенных трубопроводов начинают не ранее, чем через 24 ч после выполнения последнего соединения. Система водостоков считается выдержавшей испытание, если по истечении 20 мин после ее наполнения при наружном осмотре трубопроводов не обнаружено течи или других дефектов и уровень воды в стояках не понизился.
8.11. Пневматические испытания трубопроводов, выполненных из полимерных материалов, производят при наземной и надземной их прокладке в следующих случаях: температура окружающего воздуха ниже 0 °С; применение воды недопустимо по техническим причинам; вода в необходимом для испытаний количестве отсутствует.
Порядок пневматических испытаний трубопроводов из полимерных материалов и требования безопасности при испытаниях устанавливаются проектом.
8.12. Предварительные и окончательные испытания самотечных канализационных сетей из труб большого диаметра допускается производить пневматическим способом. Предварительные испытания проводят до окончательной засыпки траншеи (сварные соединения грунтом не засыпают). Испытательное давление сжатого воздуха, равное 0,05 МПа, поддерживают в трубопроводе в течение 15 мин. При этом осматривают сварные, клеевые и другие стыки и выявляют неплотности по звуку просачивающегося воздуха, по пузырям, образующимся в местах утечки воздуха через стыковые соединения, покрытые мыльной эмульсией.
Окончательные испытания пневматическим способом проводят при уровне грунтовых вод над трубой в середине испытуемого трубопровода менее 2,5 м. Окончательным пневматическим испытаниям подвергают участки длиной 20 - 100 м, при этом перепад между наиболее высокой и низкой точками трубопровода не должен превышать 2,5 м. Пневматические испытания проводят через 48 ч после засыпки трубопровода. Испытательное избыточное давление сжатого воздуха указано в таблице 6.
Таблица 6
Испытательное давление сжатого воздуха при пневматическом
испытании самотечных канализационных трубопроводов
Уровень грунтовых вод h от оси трубопровода, м
|
Испытательное давление, МПа
|
Перепад давления,

, МПа
|
избыточное начальное p
|
конечное
|
h = 0
|
0,01
|
0,007
|
0,003
|
0 < h < 0,5
|
0,0155
|
0,0124
|
0,0031
|
0,5 < h < 1
|
0,021
|
0,0177
|
0,0033
|
1 < h < 1,5
|
0,0265
|
0,0231
|
0,0034
|
1,5 < h < 2
|
0,032
|
0,0284
|
0,0036
|
2 < h < 2,5
|
0,0375
|
0,0338
|
0,0037
|
8.13. Приемку в эксплуатацию трубопроводов необходимо проводить, руководствуясь основными положениями
СНиП 3.01.04
, а также
СНиП 3.05.04
. При испытании трубопроводов водоснабжения и напорной канализации и сдаче их в эксплуатацию должны составляться:
- акты на скрытые работы (по основанию, опорам и строительным конструкциям на трубопроводах и т.д.);
- акты наружного осмотра трубопроводов и элементов (узлов, колодцев и т.д.);
- акты испытаний на прочность и плотность трубопроводов;
- акты на промывку и дезинфекцию водопроводов;
- установление соответствия выполненных работ проекту;
- акты входного контроля качества труб и соединительных деталей.
8.14. Кроме приемки скрытых работ и проверки актов испытания трубопроводов на плотность и наружного осмотра, приемка безнапорных трубопроводов должна сопровождаться проверкой прямолинейности, а также инструментальной проверкой лотков в колодцах.
При приемке внутренних водопроводов дополнительно производится проверка паспортов или сертификатов на полимерные трубы, соединительные детали и арматуру.
9. ТЕХНИКА БЕЗОПАСНОСТИ ПРИ МОНТАЖЕ ТРУБ
ИЗ ПОЛИМЕРНЫХ МАТЕРИАЛОВ
9.1. Общие требования техники безопасности указаны в
СНиП III-4
, кроме того, следует выполнять требования настоящего раздела.
9.2. Необходимо проводить осмотр и контроль сварочного оборудования, а также изоляции электропроводок, работы устройств для механической обработки концов и торцов труб. Результаты проверки должны соответствовать паспортным данным на оборудование.
9.3. Технический осмотр следует производить не реже, чем один раз в месяц с регистрацией результатов проверки в журнале производства работ.
9.4. Значения параметров режимов сварки должны отвечать требованиям технологических норм для каждого вида полимера.
9.5. К производству сварочно-монтажных работ при строительстве трубопроводов из полимерных материалов допускаются сварщики, прошедшие теоретическое и практическое обучение по специальной программе и сварившие контрольные стыки по специальной программе.
9.6. Трубы в процессе хранения и монтажа не выделяют в окружающую среду токсичных веществ и не оказывают влияния на организм человека при непосредственном контакте. Работа с трубами не требует особых мер безопасности.
9.7. При работе с трубами следует соблюдать правила пожарной безопасности. В случае возникновения пожара и загорания труб их следует тушить любыми средствами пожаротушения. При тушении огня от загорания труб в складских помещениях следует применять противогазы с фильтром марки "В" или фильтрующие противогазы.
9.8. Гидравлические и пневматические испытания трубопроводов следует производить после их надежного закрепления и устройства упоров по их концам и на поворотах.
9.9. При монтаже и испытаниях трубопроводов запрещается прислонять к ним лестницы и стремянки, ходить по трубопроводу. Запрещается обстукивать трубы молотком или оттягивать их от стенок траншеи или строительных конструкций.
10. ТРАНСПОРТИРОВАНИЕ И ХРАНЕНИЕ ТРУБ
ИЗ ПОЛИМЕРНЫХ МАТЕРИАЛОВ
10.1. Полимерные трубы и соединительные детали могут транспортироваться любым видом транспорта в соответствии с правилами перевозки грузов, техническими условиями погрузки и крепления грузов, действующими на данном виде транспорта, и техническими требованиями поставщика при условии обеспечения мер по предупреждению механических повреждений груза. Все работы, связанные с транспортировкой, следует проводить при температуре окружающего воздуха не ниже указанной в соответствующих нормативных документах.
10.2. Трубы из полимерных материалов рекомендуется хранить и перевозить намотанными в бухты или на катушки, отдельными упаковками в пачки или отдельными трубами большого диаметра в соответствии с нормативными документами на их изготовление.
10.3. При погрузке и разгрузке труб и деталей, особенно при отрицательных температурах воздуха и температурах, близких к нулю, необходимо соблюдать осторожность для исключения ударов и механических повреждений.
10.4. При хранении труб на складах должны соблюдаться условия, указанные в нормативных документах, при этом высота штабеля труб не должна превышать 3 м.
Хранение труб, намотанных на катушки, допускается только в вертикальном положении.
Хранение соединительных деталей должно осуществляться только в упакованном виде.
Необходимо обеспечить сохранность труб и соединительных деталей от механических повреждений, деформаций, попадания на них нефтепродуктов и жиров, засорения внутренних поверхностей, облучения солнечными лучами.
10.5. В период монтажа срок хранения труб и деталей на строительной площадке должен быть минимальным.
КЛАССИФИКАЦИЯ ТРУБ ИЗ ПОЛИМЕРНЫХ МАТЕРИАЛОВ
Для напорных труб действующие нормативные документы устанавливают соотношение между наружным диаметром и толщиной стенки труб в зависимости от максимального рабочего давления: 0,25; 0,32; 0,4; 0,6; 1; 1,6; 2; 2,5 МПа по формуле

, (А.1)
где P - максимальное рабочее давление (МОР), МПа;

- наружный диаметр трубопровода, м;
s - толщина стенки трубопровода, м;

- расчетная прочность из условия длительной прочности, МПа.
В принятой в настоящее время международной классификации маркировка труб производится по сериям "S" и стандартному отношению "SDR", значения которых определяются по формулам:

;

. (А.2, А.3)
Максимальное рабочее давление связано с "S" и "SDR" отношением
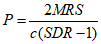
, (А.4)
где MRS - минимальная длительная прочность, МПа;
c - коэффициент запаса прочности, устанавливается для каждого вида материала и должен приводиться в соответствующих сводах правил.
Канализационные трубы подразделяются на классы по кольцевой жесткости

, кПа

, (А.5)
где

- модуль упругости материала, кПа;

- средний диаметр сечения трубы, м;

- коэффициент Пуассона материала трубы.
При

< 2500 труба считается "нежесткой", при

2500 - 5000 - "полужесткой", при

= 5000 - 10000 - "жесткой".
Основные показатели свойств некоторых полимерных материалов труб приведены в таблице А.1.
Таблица А.1
Физико-механические показатели некоторых полимерных материалов,
применяемых при производстве труб
и соединительных деталей (справочные данные)
┌──────────┬───────────────────────────────────────────────────────┐
│Показатель│ Величина показателя для материала │
│ ├─────────────┬──────┬─────┬─────┬──────┬──────┬────────┤
│ │ ПНД │ ПВД │ ПВХ │ ПП │Сшитый│Хлори-│Стекло- │
│ ├──────┬──────┤(ПНП) │ │ │поли- │рован-│пластик │
│ │ ПВП │ ПСП │ │ │ │этилен│ный │ │
│ │ │ │ │ │ │ │ПВХ │ │
├──────────┼──────┼──────┼──────┼─────┼─────┼──────┼──────┼────────┤
│Плотность,│0,94 -│0,93 -│0,91 -│1,4 │0,91 │0,93 -│1,57 │1,6 - │
│г/см3 │ 0,96│ 0,94│ 0,93│ │ │ 0,95│ │ 2,2│
├──────────┼──────┼──────┼──────┼─────┼─────┼──────┼──────┼────────┤
│Предел │20 - │15 - │10 - │50 - │25 - │18 - │50 - │40 - │
│текучести │ 25│ 18│ 12│ 56│ 28│ 26│ 55│ 200 <
*
>│
│при рас- │ │ │ │ │ │ │ │ │
│тяжении, │ │ │ │ │ │ │ │ │
│МПа │ │ │ │ │ │ │ │ │
├──────────┼──────┼──────┼──────┼─────┼─────┼──────┼──────┼────────┤
│Удлинение │800 │800 │600 │50 │>200 │200 - │70 - │0,4 - │
│при раз- │ │ │ │ │ │ 500│ 120│ 1,4│
│рыве, % │ │ │ │ │ │ │ │ │
├──────────┼──────┼──────┼──────┼─────┼─────┼──────┼──────┼────────┤
│Модуль │800 │600 │200 │3000 │1200 │550 - │2900 │5000 - │
│упругости,│ │ │ │ │ │ 800 │ │ 25000 │
│МПа │ │ │ │ │ │ │ │ <
**
> │
├──────────┼──────┼──────┼──────┼─────┼─────┼──────┼──────┼────────┤
│Коэффици- │2 │2 │2 │0,7 │1,5 │1,2 - │0,62 │0,18 - │
│ент теп- │ │ │ │ │ │ 1,4 │ │ 0,3│
│лового │ │ │ │ │ │ │ │ │
│линейного │ │ │ │ │ │ │ │ │
│расшире- │ │ │ │ │ │ │ │ │
│ния, │ │ │ │ │ │ │ │ │
│ -4 -1 │ │ │ │ │ │ │ │ │
│10 °С │ │ │ │ │ │ │ │ │
├──────────┼──────┼──────┼──────┼─────┼─────┼──────┼──────┼────────┤
│Расчетная │5 - │5 │2,5 - │10 - │5 - │6,3 │10 │10 - │
│прочность,│ 6,3│ │ 3,2│ 12,5│ 6,3│ │ │ 30 <
**
>│
│МПа │ │ │ │ │ │ │ │ │
├──────────┴──────┴──────┴──────┴─────┴─────┴──────┴──────┴────────┤
│ <*> Для фенолформальдегидных, полиэфирных и эпоксидных смол. │
│ <**> В осевом направлении. │
└──────────────────────────────────────────────────────────────────┘
ПЕРЕЧЕНЬ НОРМАТИВНЫХ ДОКУМЕНТОВ
В настоящих нормах даны ссылки на следующие нормативные документы:
СНиП 2.04.01-85*
. Внутренний водопровод и канализация зданий
СНиП 2.04.02-84*
. Водоснабжение. Наружные сети и сооружения
СНиП 2.04.03-85
. Канализация. Наружные сети и сооружения
СНиП 2.04.14-88*
. Тепловая изоляция оборудования и трубопроводов
СНиП 2.07.01-89*
. Градостроительство. Планировка и застройка городских
и сельских поселений
СНиП 3.01.01-85*
. Организация строительного производства
СНиП 3.01.04-87
. Приемка в эксплуатацию законченных строительством
объектов. Основные положения
СНиП 3.05.01-85*
. Внутренние санитарно-технические системы
СНиП 3.05.04-85*
. Наружные сети и сооружения водоснабжения и канализации
СНиП III-4-80*
. Техника безопасности в строительстве
ГОСТ 2930-62
. Приборы измерительные. Шрифты и знаки
Взамен ГОСТ 18599-83 Постановлением Госстандарта РФ от
23.03.2002 N 112-ст с 1 января 2003 года введен в действие
ГОСТ 18599-2001
.
ГОСТ 18599-83. Трубы напорные из полиэтилена. Технические условия
Взамен ГОСТ 29324-92 Приказом Ростехрегулирования от
05.10.2004 N 24-ст с 1 апреля 2005 года введен в действие
ГОСТ ИСО 161-1-2004
.
ГОСТ 29324-92. Трубы из термопластов для транспортирования
(ИСО 161/1-78) жидкостей. Номинальные наружные диаметры и
номинальные давления. Метрическая серия.
(справочное)
НОМОГРАММЫ ДЛЯ ОПРЕДЕЛЕНИЯ ПОТЕРЬ НАПОРА В ТРУБАХ
Рисунок В.1. Номограмма для определения потерь напора
в трубах диаметром 6 - 100 мм (при

= 0,00002)
Рисунок В.2. Номограмма для определения потерь напора
в трубах диаметром 100 - 1200 мм (при

= 0,00002)
Рисунок В.3. Номограмма для определения поправочного
коэффициента

на температуру воды при расчете
труб диаметром 6 - 100 мм
Рисунок В.4. Номограмма для определения поправочного
коэффициента

на температуру воды при расчете
труб диаметром 100 - 1200 мм
(справочное)
ДЛЯ ОПРЕДЕЛЕНИЯ ДИАМЕТРА КАНАЛИЗАЦИОННОГО ТРУБОПРОВОДА
Рисунок Г.1. Номограмма для определения диаметра
канализационного трубопровода
МЕТОДИКА ПРОЧНОСТНОГО РАСЧЕТА ТРУБОПРОВОДОВ ИЗ ПОЛИМЕРНЫХ
МАТЕРИАЛОВ ПРИ ПОДЗЕМНОЙ ПРОКЛАДКЕ (ОБЩИЕ ПРИНЦИПЫ)
Прочностной расчет трубопроводов из полимерных материалов, уложенных в земле, рекомендуется сводить к соблюдению неравенства:
для напорных трубопроводов
; (Д.1)
для самотечных трубопроводов
; (Д.2)
для дренажных трубопроводов
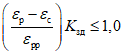
, (Д.3)
где

- максимальное значение деформации растяжения материала в стенке трубы из-за овальности поперечного сечения трубы под действием грунтов (

, МПа) и транспортных нагрузок (

, МПа);

- степень растяжения материала стенки трубы от внутреннего давления воды в трубопроводе;

- степень сжатия материала стенки трубы от воздействия внешних нагрузок на трубопровод;

- предельно допустимое значение деформации растяжения материала в стенке трубы, происходящей в условиях релаксации напряжений;

- предельно допустимая деформация растяжения материала в стенке трубы в условиях ползучести;

- коэффициент запаса, учитывающий вид перфорации в стенках трубы, который можно принять при круговом отверстии в гладкостенной трубе - 2,3; круговом отверстии в стекло- (базальто)пластиковой трубе - 3,0; щелевом отверстии со скругленными углами (соотношение сторон 8:1, например, 25 на 3) - 1,3; для других условий величина

должна приводиться в нормативных документах.
Значение

может быть определено по формуле
, (Д.4)
где

- коэффициент постели грунта для изгибающих напряжений, учитывающий качество уплотнения, его можно принимать: при тщательном контроле - 0,75, при периодическом контроле - 1,0, при отсутствии контроля - 1,5;

- коэффициент запаса на овальность поперечного сечения трубы, принимается равным: 1,0 - для напорных и самотечных трубопроводов и 2 - для дренажных трубопроводов;

- относительное укорочение вертикального диаметра трубы в грунте, устанавливается как предельно допустимое значение
, (Д.5)
где

- относительное укорочение вертикального диаметра трубы под действием грунтовой нагрузки;

- то же, под действием транспортных нагрузок;

- относительное укорочение вертикального диаметра трубы, образовавшееся в процессе складирования, транспортировки и монтажа. Его можно приближенно принимать по таблице Д.1.
Кольцевая жесткость

оболочек трубы, Па
|

при степени уплотнения грунта
|
до 0,85
|
0,85 - 0,95
|
более 0,95
|
До 276000
|
0,06
|
0,04
|
0,03
|
276000 - 290000
|
0,04
|
0,03
|
0,02
|
Больше 290000
|
0,02
|
0,02
|
0,01
|
, (Д.6)
где

- коэффициент, учитывающий запаздывание овальности поперечного сечения трубы во времени и зависящий от типа грунта, степени его уплотнения, гидрогеологических условий, геометрии траншеи, может принимать значения от 1 до 1,5;

- коэффициент прогиба, учитывающий качество подготовки ложа и уплотнения, можно принимать: при тщательном контроле - 0,09, при периодическом - 0,11, при бесконтрольном ведении работ - 0,13;

- коэффициент, учитывающий влияние грунта засыпки на овальность поперечного сечения трубопровода, можно принять равным 0,06;

- модуль деформации грунта в пазухах траншеи, МПа;

- коэффициент, учитывающий влияние кольцевой жесткости оболочки трубы на овальность поперечного сечения трубопровода, можно принимать равным 0,15;

, (Д.7)
где

- удельный вес грунта, Н/м3;

- глубина засыпки трубопровода, считая от поверхности земли до уровня горизонтального диаметра, м;

- кратковременная кольцевая жесткость оболочки трубы, МПа;
, (Д.8)
где

- кратковременный модуль упругости при растяжении материала трубы, МПа;
I - момент инерции сечения трубы на единицу длины, определяемый по формуле
, (Д.9)

- коэффициент Пуассона материала трубы, приводится в нормативной документации;
, (Д.10)
где

- коэффициент уплотнения грунта;

- транспортная нагрузка, принимаемая по справочным данным для гусеничного, колесного и другого транспорта, МПа;
n - коэффициент, учитывающий глубину заложения трубопровода, при H < 1 n = 0,5;

- коэффициент, учитывающий процесс округления овализованной трубы под действием внутреннего давления воды в водопроводе (Р, МПа)
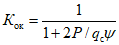
, (Д.11)
где

- суммарная внешняя нагрузка на трубопровод, МПа;

; (Д.12)

; (Д.13)
; (Д.14)
, (Д.15)
где

- кратковременная расчетная прочность при растяжении материала трубы, МПа;

,

- кратко- и долговременное значения модуля упругости при растяжении материала трубы на конец срока службы эксплуатации трубопровода, МПа.
, (Д.16)
где

- коэффициент запаса, должен приводиться в нормативных документах.
Если в результате расчетов значение левой части выражения (
Д.1
) будет больше 1, то следует повторить расчеты при других характеристиках материала труб или укладки трубопровода.
Далее проверяют устойчивость оболочки трубы против действия сочетания нагрузок: для напорных сетей - грунтовые и транспортные

, от грунтовых вод,

, а также возможного возникновения вакуума

в трубопроводе, для самотечных сетей -

+

, для дренажных сетей - с использованием выражения
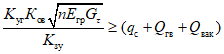
, (Д. 17)
где

- коэффициент, учитывающий влияние засыпки грунта на устойчивость оболочки, можно принять 0,5, а для соотношения

:

= 4:1 - равным 0,07;

- коэффициент, учитывающий овальность поперечного сечения трубопровода, при
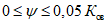
= 1 - 0,7

;

- коэффициент запаса на устойчивость оболочки на действие внешних нагрузок, можно принять равным 3;

- длительная кольцевая жесткость оболочки трубы, МПа, определяется по формуле
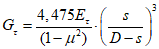
. (Д.18)
Пример расчета на прочность подземного канализационного трубопровода
Дано. Трубы с наружным диаметром 1200 мм, ПНД, среднелегкого типа с толщиной стенки s = 46,2 мм (ГОСТ 18599) укладываются в траншею на глубину

= 5 м в сети самотечной канализации. В условиях строительства по поверхности над трубопроводом возможно перемещение тяжелого транспорта с давлением на грунт

= 0,01 МПа. Высота грунтовых вод - 1 м от поверхности земли. Требуется подобрать грунт для засыпки.
Решение. Для засыпки на месте строительства принимаем грунт с удельным весом

= 18 кН/м3. Значения кратко- и долговременного модулей упругости ПНД -

= 800 МПа и

= 200 МПа.
1. Определяем грунтовую нагрузку

=

= 18 х 5 = 90 кН/м2 = 0,09 МПа.
2. Определяем общую нагрузку

=

+

= 0,09 + 0,01 = 0,1 МПа.
3. Определяем кратковременную кольцевую жесткость оболочки трубы по (
Д.8
,
Д.9
)

МПа.
4. Определяем относительное укорочение вертикального диаметра трубы под действием грунтовой нагрузки по (
Д.6
) при

= 1

или 3,7%,
принимаем

- как среднее значение, равным 1,25;

- с учетом периодического контроля равным 0,11;

- равным 0,15;

- равным 0,06;

- равным 5 МПа (для средних условий).
5. Определяем укорочение вертикального диаметра трубы под действием транспортной нагрузки по (
Д.10
)

или 0,3%.
6. Определяем относительное укорочение вертикального диаметра трубы по (
Д.5
), приняв

= 2% (для

> 0,29 МПа и степени уплотнения грунта 0,85 - 0,95 по
таблице Д.1
)

.
7. Определяем максимальное значение степени растяжения материала в стенке трубы из-за овальности поперечного сечения трубопровода под действием нагрузок по (
Д.4
) при

= 1 м

;

или 1%.
8. Определяем степень сжатия материала стенки трубы, происходящего под действием внешних нагрузок на трубопровод по (
Д.14
)

или 0,16%.
9. Определяем допустимую степень растяжения материала в стенке трубы, происходящего в условиях релаксации по (
Д.15
) при

= 25 МПа
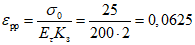
или 6,25%.
10. Определяем допустимую степень растяжения материала в стенке трубы, происходящего в условиях ползучести по (
Д.16
)
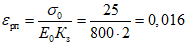
или 1,6%.
11. Проверяем прочность по (
Д.2
)

, что меньше 1,
т.е. принятые данные по грунту засыпки и его уплотнения удовлетворяют прочностным требованиям для данного трубопровода.
О ПРОВЕДЕНИИ ВХОДНОГО КОНТРОЛЯ ПАРТИИ ТРУБ
ИЗ ПОЛИМЕРНЫХ МАТЕРИАЛОВ (СОЕДИНИТЕЛЬНЫХ ДЕТАЛЕЙ)
полученных _______________________________________________________
наименование организации получателя
Трубы (соединительные детали) получены для систем ____________
_____________________________ давлением _______________ МПа.
водопровод, канализация и др.
Мы, нижеподписавшиеся, комиссия в составе:
представители ________________________________________________
организация заказчика, должность, Ф.И.О
__________________________________________________________________
организация подрядчика, должность, Ф.И.О
__________________________________________________________________
эксплуатирующая организация, должность, Ф.И.О
провели входной контроль партии труб (соединительных деталей) N __
диаметром _________________ мм, длиной __________________ м (шт.),
поставленных _____________________________________________________
наименование фирмы, дата
из полимера типа ________________________________________________.
Партия состоит из ____________________________________________
шт., бухт или барабанов (ящиков
_______________________ и соответствует __________________________
соединительных деталей) российский или
____________________
зарубежный стандарт
Количество труб Д
У __ мм, длиной __ м _______________________.
(маркировка по стандарту)
Количество деталей Д
У ___ мм ___ шт. ________________________.
(маркировка по стандарту)
Данные о сопроводительном сертификате ________________________
Результат: партия труб (соединительных деталей) соответствует
(не соответствует) российским стандартам и сопроводительным
сертификатам и может (не может) быть допущена к монтажу.
Дата Подписи
От заказчика _______________
От подрядчика ______________
От эксплуатирующей
организации ________________